Se esiste sul mercato un “oggetto” in grado di schiudere interi mondi, questo è sicuramente lo pneumatico: un vero e proprio portale al di là del quale si estendono tematiche ampie e diversificate, dall’infinitamente piccolo, da studiare e osservare con strumenti di indagine avanzati, fino alla sicurezza da garantire a chi si trovi a frenare, magari anche in condizioni stradali non ottimali, un mezzo da 40 tonnellate.
Tutti argomenti che Michela Caprio, Responsabile R&D Materiali Prometeon Tyre Group, padroneggia con la sicurezza e la grazia di una moderna alchimista abituata a sperimentare per ottenere esattamente la formula giusta. “Sono di origine campana – inizia a raccontarci la manager – sono nata ad Avellino e mi sono laureata in chimica all’Università di Salerno. Ho sempre seguito la mia passione e in questo percorso ho avuto la fortuna di incontrare aziende che hanno creduto in me”.
“Agli esordi sono stata contattata da una compagnia americana quando ancora ero impegnata con “i miei magheggi” in laboratorio, intenta a mettere a punto la tesi sperimentale. Poi, in seguito al master di specializzazione, condotto sempre all’interno del mondo degli pneumatici, sono stata avvicinata ad un convegno da un responsabile Pirelli, e dagli Stati Uniti mi sono trasferita a Milano, dove mi sono occupata per il brand dello sviluppo mescole moto, per poi passare in Prometeon nel 2017”.
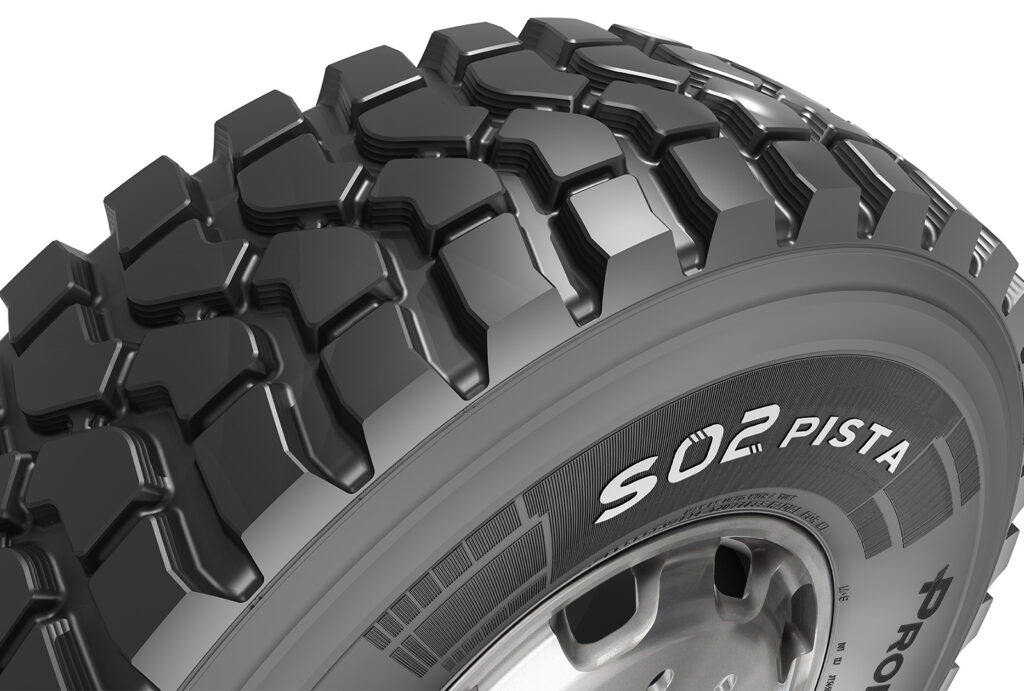
“Ho sempre lavorato su materiali e innovazione, e oggi nella mia area ci interessiamo del mondo micro, dello sviluppo dei componenti, delle mescole e di tutto il processo che porta alla realizzazione di uno pneumatico, dall’arrivo in fabbrica delle materie prime fino alla vulcanizzazione, passando per il mixing, e finendo con il controllo del prodotto finito”.
L’importanza dei materiali
Il team che fa capo a Michela consiste di ricercatori chimici al lavoro sia nell’headquarter lombardo sia nei centri di ricerca che si trovano presso i siti produttivi di Prometeon in Egitto, Turchia e Brasile. “In realtà – prosegue Michela – non ci interessiamo solo del confezionamento del prodotto, ma soprattutto di ciò che succede prima: seguiamo il contatto con i fornitori, e curiamo soprattutto lo scouting sul mercato alla ricerca di materiali innovativi, di tutte le idee ‘out of the box’ in grado di apportare cambiamento e innovazione all’interno del nostro mondo”.
“Materiali che normalmente vengono utilizzati in contesti completamente diversi, e mi viene in mente l’edilizia o la cosmesi, ingredienti che fino ad ora sono stati estranei al metodo tradizionalmente utilizzato per preparare le mescole, ma che noi oggi vediamo in grado di conferire un grado maggiore di efficienza ai nostri pneumatici”.
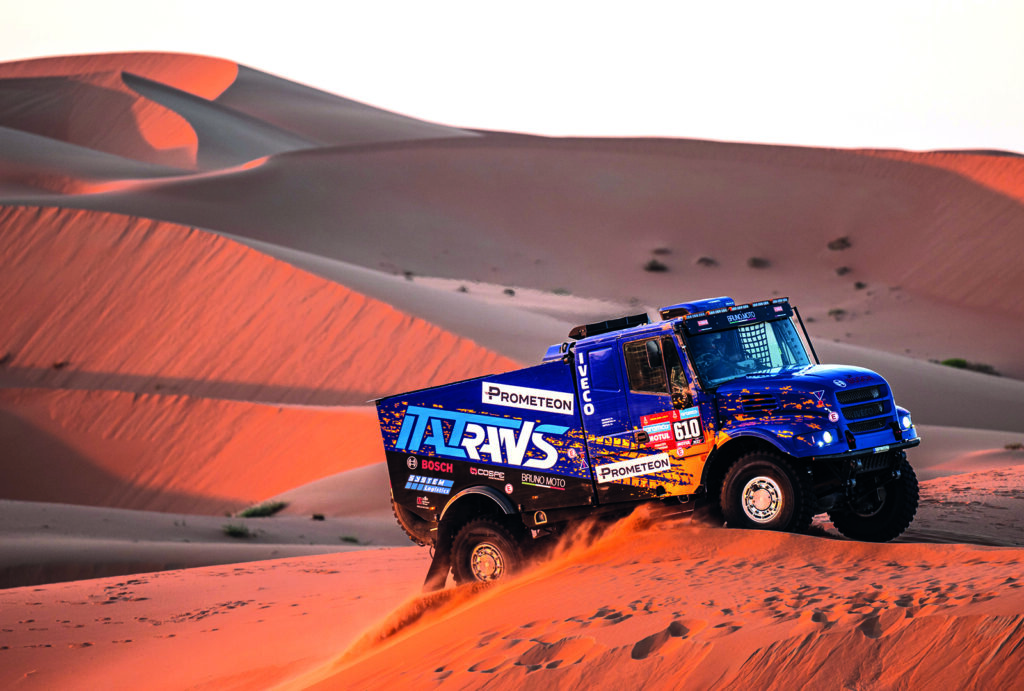
“Si tratta di idee e spunti che arrivano non solo da riflessioni interne o da sviluppi delle nostre attività, ma anche e soprattutto dal confronto con l’ambiente esterno, con i fornitori, e anche con i clienti, che si dimostrano sempre più consapevoli, esigenti e attenti, anche alle caratteristiche tecniche dei prodotti”.
Una predisposizione alla ricerca e all’innovazione che Prometeon sviluppa fin dalla sua nascita e che si rinforza di giorno in giorno, con la consapevolezza che il cambiamento non si realizza in tempi brevi, ma deve essere una tensione costante nella quale credere, investire e lavorare quotidianamente.
“È importante dedicare attenzione agli input e ai suggerimenti che arrivano dall’esterno, acquisire conoscenze, informazioni, intessere relazioni: il nostro know-how è basato anche e grandemente sulle collaborazioni che intratteniamo con enti esterni, università e start-up, e sugli accordi di co-sviluppo con i nostri fornitori. Basti pensare che solo nella nostra area ne contiamo più di una ventina, e sono ossigeno per noi, perché ci regalano la possibilità di sperimentare prospettive diverse”.
La Serie 02 di Prometeon
Quando parliamo con Michela di innovazione, il riferimento temporale non è solo il futuro: già oggi la gamma Prometeon ha raggiunto risultati eccellenti quanto all’impiego di materiali che sono sì sostenibili, ma garantiscano al tempo stesso all’utilizzatore performance inalterate o addirittura migliori. La Serie 02, lanciata un anno e mezzo fa, si articola su prodotti completamente rinnovati rispetto a quella che è stata fin qui nel settore dei veicoli industriali la concezione dello pneumatico. “È stata proprio questa – spiega meglio Caprio – la scelta di Prometeon: ricominciare da capo e realizzare qualcosa di completamente diverso, pensato dalle nostre persone”.
La Serie 02 presenta già, sia lato materiali che lato processo, profonde innovazioni: i pneumatici Prometeon propongono infatti al loro interno un’alta percentuale di gomma naturale, un elastomero che aiuta nelle performance, in particolare in riferimento alla capacità del prodotto di resistere alla lacerazione e all’abrasione. “Abbiamo scelto di utilizzarne una percentuale molto alta, trovando il giusto bilanciamento tra le prestazioni finali e le opportunità date da un ingrediente naturale, che utilizziamo osservando una severa policy relativa alla protezione delle foreste e alla sostenibilità di tutta la catena di approvvigionamento”.
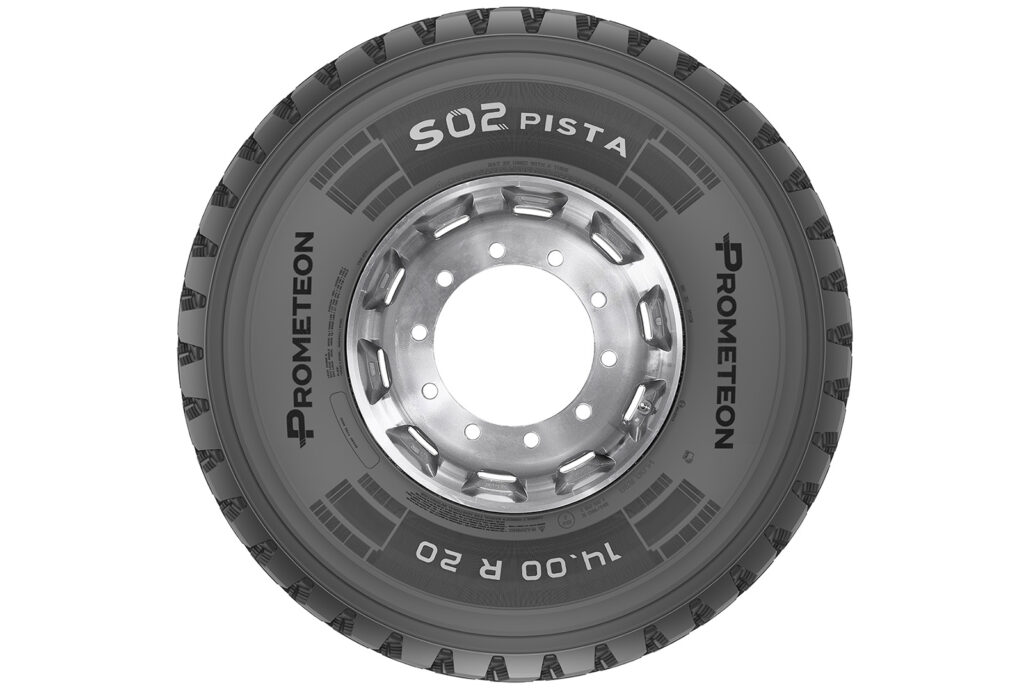
“Sì, la nostra scelta è stata quella di ridurre l’utilizzo di materiali che derivano dal mondo del petrolio. Ovviamente non abbiamo ancora tagliato il traguardo di questa sfida, ma già oggi circa il 33 per cento dei componenti dei nostri pneumatici ha un carattere di sostenibilità, perché sono naturali o riciclati: in quest’ultimo caso in particolare quella che realizziamo è una vera e propria economia circolare. Sappiamo bene che gli pneumatici dismessi presentano il conto di un notevole impatto ambientale: noi li polverizziamo e impieghiamo questi scarti per produrre energia o per “cucinare” nuove coperture”.
Obiettivo incrementare la percentuale di materiali sostenibili
Il target di Prometeon per il 2030 è di incrementare la percentuale di materiali sostenibili all’interno degli pneumatici fino al 40 per cento. “Stiamo parlando – precisa Michela Caprio – di tutta la produzione, quindi di tutto ciò che esce dalle linee di ogni nostro impianto, in tutto il mondo, e vi assicuro che non è una conversione semplice da mettere a terra. Questa sarà la soglia minima, al di là della quale lanceremo anche famiglie di prodotti con quote di materiali sostenibili più alte, fino all’ottanta per cento”.
“Ma vorrei essere chiara su un punto: una quantità così elevata di materiali sostenibili su tutta la produzione oggi non è ipotizzabile, ma non tanto per nostri limiti tecnologici, quanto per indisponibilità di risorse. Tutti i settori dell’economia si stanno riorganizzando intorno alla transizione ecologica: non solo noi e i nostri competitor, è il mondo ad essere chiamato ad un cambiamento radicale, e questo determina una scarsità dei materiali. Poi esiste il tema dell’attenzione che dobbiamo prestare, e che prestiamo, alla filiera: i materiali che acquistiamo dai nostri fornitori devono essere certificati e vagliati da audit di terze parti per un controllo assoluto e costante”.
“Dobbiamo essere sicuri oltre ogni dubbio di ciò che utilizziamo e dell’intera supply chain”. “Io mi rendo conto – prosegue Michela – che lo pneumatico è una “cosa” nera che rotola sulla strada, e quindi non è immediato comprendere la complessità dei processi sottostanti. E l’argomento si fa ancora più articolato per noi che proviamo a riscrivere continuamente la formulazione dei prodotti cercando di soddisfare un doppio input: da una parte introdurre materiali innovativi e sostenibili e dall’altra incrementare le performance”.
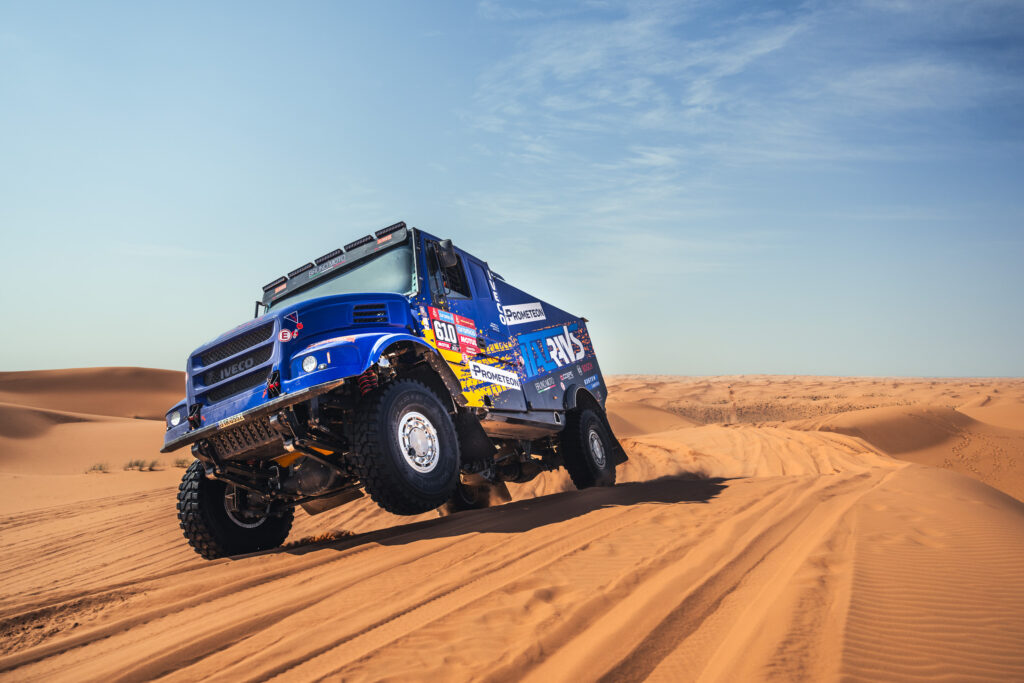
“Quando si tratta di pneumatici per veicoli industriali i riferimenti che definiscono le prestazioni sono tenuta sul bagnato, resistenza al rotolamento, all’abrasione e alla lacerazione: è un tema di costi, perché uno pneumatico che performa meglio dura di più, ma anche e soprattutto, com’è intuibile, di sicurezza. Inoltre c’è da considerare che le gomme truck vengono anche ricostruite con la sostituzione del battistrada: ma la carcassa rimane, quindi quando formuliamo un prodotto dobbiamo pensare non a farlo vivere una volta, ma almeno due”.
Ottimizzazione dei processi
Sotto la lente non c’è solo la composizione del prodotto: il team di Michela prende in considerazione senza sosta anche l’ottimizzazione dei processi che portano alla realizzazione delle coperture, testando metodi differenti per il mixing o la vulcanizzazione. “Per dare l’idea di un numero – conclude Michela – se immaginassimo di tagliare uno pneumatico e di guardarlo al microscopio, vedremmo fino a quindici parti diverse”.
“Ognuna di queste mescole può presentare più di 15 ingredienti, e tutti questi materiali devono comunicare tra loro, essere armonici, esattamente come in cucina quando si esegue una ricetta: anche nei nostri impianti gli ingredienti devono cuocere contemporaneamente per dare il prodotto finale con le giuste proprietà e le caratteristiche che servono ai nostri clienti. Che, del gioco di sostituzioni, non devono accorgersi di nulla, se non di un incremento delle prestazioni: solo ottenendo questo risultato il nostro percorso avrà avuto un senso, e la “torta” sarà un successo”.